Validation & Verification in Medical Device Design for Patient Safety
🔊 Listen to the Summary of this article in Audio
FDA’s 21 CFR Part 820.3 explains verification clearly. It’s the act of confirming through tests and solid evidence that a medical device meets the required standards. Such an essential step shields patient safety by making sure the device’s final design meets the original expectations. Validation and verification are key in the medical device field, ensuring products are both high-quality and safe.
The FDA highlights validation’s role too. It’s the process of checking with evidence that a device meets its purpose for specific use. It shows that the device operates as expected in real life, considering how it’s used, where it’s used, and who uses it. It even looks at packaging and how it’s labeled, checking everything for safety and effectiveness from start to finish.
Start planning for verification and validation at the beginning. Waiting too long can hurt your chance of meeting regulatory standards on time. This could lead to products being recalled or legal issues. To avoid such problems, a quality management system like Greenlight Guru helps. It organizes design tasks, links documents, and ensures everything is traceable, making the whole development process smoother.
Key Takeaways
- Design verification confirms that design outputs meet design inputs, ensuring regulatory compliance.
- Validation ensures medical devices fulfill their intended use and meet user needs under actual conditions.
- Starting early with verification and validation planning is critical to avoid regulatory delays and non-compliance.
- Utilizing quality management systems can improve centralized control and documentation, aiding in regulatory adherence.
- Incorporating lessons from past verification and validation efforts can enhance future device designs.
Importance of Validation and Verification for Patient Safety
Validation and verification are key to safety in medical devices. They make sure devices work safely and as they should. These steps follow strict rules to show devices are safe for use.
Ensuring Compliance with Regulatory Standards
Following regulatory standards is a must in making medical devices. Design verification and validation check that designs meet set requirements and final devices meet user needs. Design verification might include benchtop tests or inspections to check quality. Design validation, on the other hand, tests devices in real or simulated environments to find any flaws.
Process | Main Activities | Purpose |
---|---|---|
Design Verification | Benchtop Testing Analysis Inspection | Confirms design outputs meet design inputs |
Design Validation | Simulated Use Testing Actual Use Testing Human Factors Validation | Ensures devices conform to user needs and intended uses |
Role of FDA in Medical Device Validation
The FDA requires manufacturers to rigorously validate their medical devices. They must follow FDA 21 CFR 820.30, showing devices are safe and work well. This involves detailed testing plans and statistical methods to ensure compliance with design standards. Following these guidelines helps prevent problems after the product goes to market.
Verification and validation are essential for safe, compliant medical devices. They confirm devices meet design requirements and are safe for users. This process is crucial for adhering to regulatory standards.
Our expert team can help you implement a robust quality management system tailored to your medical device project, ensuring regulatory compliance and efficiency.
Exploring Design Verification and Design Validation
In medical device making, both design verification and validation are key. They make sure the device is safe and works well. Let’s look at how they differ and their roles.
Design Verification vs. Design Validation
Design verification makes sure the device meets the original plans. The FDA says it checks if the requirements are met. Design validation, however, checks if the device meets user needs and its intended use. It’s about making sure we made the right device.
Key Differences Between Verification and Validation
Verification and validation differ in focus. Verification matches design outputs to inputs through tests. Validation tests the device in real conditions, like clinical trials, to meet user needs.
Purposes of Design Verification and Validation
Design verification and validation are vital in developing medical devices. Verification confirms the design meets requirements. Validation ensures the device fits user needs and works as expected. It also prevents poor user experiences by confirming the product’s relevance.
Roles of Verification and Validation in Productd Development
Verification and validation are crucial in making medical devices. Verification checks if the design follows plans. Validation checks if the device works in the real world. This helps the product meet real needs and aligns with business goals. They ensure the device works well for users.
The Design and Development Process for Medical Devices
Creating medical devices is a complex process. It ensures patient safety and meets regulatory standards. This process begins with understanding the basic design needs. It moves through strict control activities, creating a comprehensive Design History File (DHF), and detailed design reviews.
Understanding Design Inputs and Outputs
Design inputs and outputs are key in making medical devices. Inputs cover user needs, regulation demands, and safety concerns. These help define how the device will perform, its safety analysis, and how user-friendly it is. Outputs are the physical results from these inputs. They include detailed drawings and the manufacturing steps needed for the device to work correctly. These must be checked and confirmed.
Design Control Activities
Design control activities guide the whole creation process of medical devices. The regulations require firms to have detailed procedures that match the device’s complexity and risks. These tasks help fix any unclear or conflicting requirements early on. They align design inputs with outputs. Regular checks for risks help find and reduce potential problems. This boosts the product’s safety and effectiveness.
Design History File
A Design History File (DHF) keeps a complete record of the design process. It includes all design activities, decisions, and changes. It ensures there is a clear record from start to end. The DHF contains only approved design outputs. This is crucial for regulatory reviews and shows the design meets all needed standards. It also helps with the design’s verification and validation.
Our custom software solutions can help you maintain comprehensive, organized Design History Files, simplifying regulatory reviews and ensuring traceability.
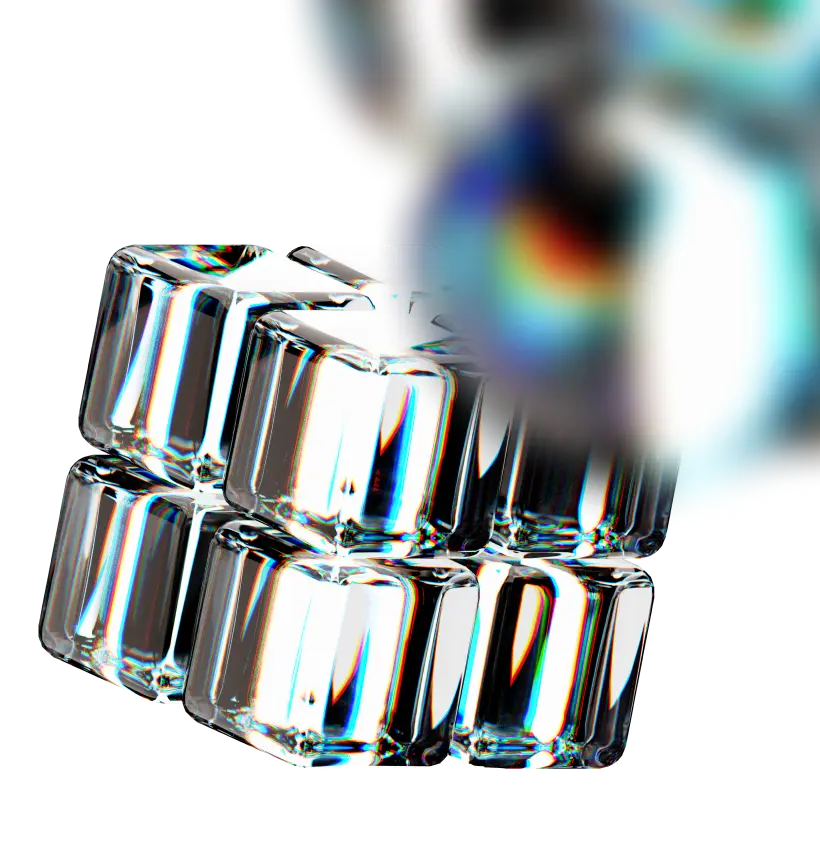
Design Review
A design review is a thorough check of the design at different development stages. It checks if the design inputs have been properly turned into outputs. The review looks at how the device performs, its risk management, and if it meets regulatory needs. Regular reviews keep the design on track, fixing any issues early. This not only meets regulations but also increases the device’s quality and reliability.
Design Verification Process
The design verification process is key to medical device integrity. It checks that the final product meets the original specs and inputs. This is done through a series of activities and tests. Every design input, like drawings and instructions, is matched with the outputs. This ensures accuracy and meets regulatory standards.
Basics of Design Verification
Design verification makes sure no detail is missed. It provides clear proof that the product’s design hits all the specifications set at the start. Through inspection, testing, and reviewing, it’s confirmed that everything aligns with requirements and regulations.
Verification Activities and Testing
Verification mixes inspections, tests, and analyses. It’s about making sure design outputs meet requirements. Tests could include seeing how a device works in tight spaces. This gives solid evidence that the device works as it should.
Verification might also use First Article Inspections or PPAP. These help check compliance with the design inputs.
Verification Focuses on Device Specifications
The main goal of design verification is to confirm device specs are accurate. It ensures the device meets standards and regulations. Developers must clearly define what the device does, its conditions, and how it will be tested. The FDA highlights the need for this step. It’s how developers make sure the device meets user needs.
Acceptable Verification Activities
Verification can involve various methods. These include trials, user tests, and studies on process capability. Each method is chosen to prove that the device meets all requirements, prepping it for validation. This stage is crucial. It answers important questions about the design and heads off problems early.
Design Validation Process
The design validation process is a crucial step in creating medical devices. The FDA says it’s about proving that device specs match user needs and intents. It makes sure the device does what it’s supposed to do, under real-world conditions.
Establishing by Objective Evidence
The validation process involves tests, inspections, and analyses. These actions provide solid proof that the design meets user needs and regulatory standards. Good planning and implementation save time and avoid mistakes.
Validation Tests and Test Suites
Validation tests for medical devices are done on actual or equivalent units. This simulates real usage. A well-chosen set of test cases ensures the device’s performance and reliability are checked thoroughly. These tests prove the product works as it should.
Validation Ensures Design Meets User Needs
The main goal of validation is to meet user needs. It’s not just about meeting technical specs. It’s also making sure the device works well in real users’ hands. Usability testing allows real users to try the device in real or simulated conditions.
Validation Activities for Medical Devices
Validation activities can include tests using the device on cadavers or clinical trials with doctors. They also look at packaging and labeling. Everything must meet the required criteria. This approach checks that the product is right for its intended use.
In the end, design validation is vital to ensure medical devices meet all user needs and regulations before they are sold. By focusing on objective evidence and thorough testing, the medical device industry protects patient safety and satisfaction.
Best Practices for Validation and Verification in Medical Device Design
The path to securing the safety and performance of medical devices follows rules like the FDA’s 21 CFR Part 820 and ISO 13485. It’s vital for manufacturers to master key validation and verification processes. These steps ensure devices are reliable and meet industry standards.
Design Control Guidance for Medical Device Manufacturers
Following expert advice, such as that from Greenlight Guru, improves compliance. It involves creating clear, actionable, and testable design inputs. These inputs lay the groundwork for checking designs against both regulatory and user needs.
Ensuring Design Meets Specified Requirements
Meeting design requirements is critical in both validation and verification. Understanding design inputs and applying strict testing is necessary. Verification checks if designs meet set requirements, while validation confirms they fit the user’s needs and uses. This includes tests and clinical studies specific to each process.
Objective Evidence and Documentation
Clear evidence and records are needed to show compliance with FDA and ISO standards. This documentation makes the design process transparent and traceable. It includes details from electronics to biological components.
Companies focus on validation and verification to boost product safety, effectiveness, and quality. By sticking to top practices, using design control guidance, and ensuring solid evidence and records, firms can effectively meet regulatory demands. This leads to the delivery of high-standard medical devices.
Common Challenges in Validation and Verification
Validation and verification face lots of challenges. Regulatory compliance is a big one due to changing standards and different needs in various places. Keeping up requires a hands-on approach. Updates, feedback, and issues must shape the design even after it hits the market.
Yet, these changes shouldn’t shake the core of V&V. Each change calls for a fresh look at user needs and design. Documenting everything well helps track changes. It keeps things clear for those who set the rules and those interested in the product. By doing this, makers can keep innovating while sticking to the rules.
Addressing Regulatory Compliance Issues
Dealing with regulatory compliance means matching up with shifting standards and needs that vary worldwide. It’s key to making sure a product matches design specs and works right, tackling verification challenges in medical tools. For prototypes, keeping clock rates in sync and using high-speed techniques is critical. This ensures they meet the needed speed for actual interfaces.
Managing Design Changes and Updates
Handling design changes and updates is tricky. It calls for a fine line between new ideas and rule-following. New challenges in updates make us look closely at validation and verification again. FPGA-based prototypes are essential here, confirming that changes don’t mess with the system’s needs or design specs.
Each change means reassessing timing and connections to avoid delays in validation. This keeps complex designs moving smoothly.
Aspect | Verification | Validation |
---|---|---|
Objective | Ensure product meets design specifications | Ensure product meets user needs |
Challenges | Initial requirement documentation, communication barriers, lack of resources | Replicating real-world usage, late-stage findings, efficient modeling of user behaviors |
Importance | Catch issues early, reduce costs, meet specified requirements | Enhance user experience, protect brand image, ensure real-world functionality |
Ensuring Thorough Documentation
Good documentation is crucial for handling rules and changes in design. It makes things clear and tracks every change. This meets the needs of those making the rules and those interested. Skipping steps in verification can break rules. Not enough validation can cause user issues, bottlenecks, or compatibility trouble. This harms product quality and how satisfied users are.
Let our experienced team develop tailored software tools to streamline your design validation and verification activities, ensuring regulatory compliance and product excellence.
Conclusion
In the world of medical device design, understanding the difference between design verification and validation is crucial. These processes are very important. They ensure that medical devices are safe for patients and build trust in medical technology. Verification checks that a device meets its specific requirements. Validation makes sure it works well in real-world use.
These processes play a key role throughout the device’s creation. They help in meeting regulations, managing risks, and providing clear documentation. Verification involves steps like checking design documents and inspections to catch mistakes early. This saves time and money. On the other side, validation tests the device to see if it meets users’ needs through detailed testing.
Looking forward, the medical device industry focuses on strong verification and validation. This approach doesn’t just meet standards; it aims to go beyond them. Embracing these rigorous processes leads to high-quality products and enhances patient safety. It shows that a manufacturer cares about leading in trust and innovation. Following these best practices from the start guarantees success in medical device design.
FAQs
What is the importance of validation and verification in medical device design?
Validation and verification are key to making sure medical devices are safe and meet regulations. Validation checks if the device fits its intended use. Verification confirms it meets design specs.
How does the FDA regulate medical device validation?
The FDA has strict rules for medical device validation. Manufacturers must prove their devices are safe and work as intended. This ensures products are consistent and risks are minimized.
What are design inputs and outputs in medical device development?
Design inputs outline what the device must do, based on user needs. They cover how it should function and its safety requirements. Design outputs are the actual designs or specs that come from these requirements. It’s important to keep these aligned from start to finish.
What is the difference between design verification and design validation?
Design verification checks if the device meets set specs and inputs. Design validation checks if the device meets user needs and works in real life. Both steps are critical for ensuring the device’s effectiveness and safety.
What activities are involved in the design verification process?
Design verification involves several steps, like inspections, analyses, and tests. These steps confirm the device matches its design specs. They provide solid proof that the device is built correctly.
How does design validation ensure a device meets user needs?
Design validation tests the device in situations similar to real life. This ensures the device meets user needs and its intended use. It involves detailed testing to fully assess the device.
What is the purpose of a Design History File (DHF) in medical device development?
The DHF is a record of the device’s development process. It shows how design inputs and outputs were managed. This helps ensure all steps meet regulatory standards.
What are some common challenges in validation and verification for medical devices?
Common issues include keeping up with regulations, handling design changes, and documenting everything properly. A good strategy for handling these challenges is essential.
What best practices should be followed for validation and verification in medical device design?
Best practices involve following design control guidance and having clear, testable design inputs. It’s also key to keep detailed records and ensure design outputs meet all requirements. These practices help ensure devices are compliant and high quality.